Physical and chemical properties of inert ceramic balls | |||||||
Element | Al2O3 % | 60 | 70 | 80 | 90 | 95 | 99 |
Fe2O3 % | ≤0.9 | ≤0.8 | ≤0.6 | ≤0.4 | ≤0.3 | ≤0.1 | |
The remaining components can be determined through negotiation between the supplier and the buyer when necessary. | |||||||
water absorption,% | 3±1,It can also be determined by negotiation between the supplier and the buyer | ||||||
proportion,kg/m³ | 2.5-3.0 | 2.7-3.2 | 2.9-3.2 | ≥3.1 | ≥3.2 | ≥3.4 | |
Bulk density,kg/m³ | 1400-1550 | 1400-1650 | 1500-1800 | 1700-1950 | 1800-1950 | ≥1900 | |
Dust, crack or break | A single bag is less than 5% | ||||||
Size deviation | Uniform sphere, the ratio of the largest to smallest diameter of a ceramic sphere does not exceed 1.2 | ||||||
Dimensional tolerance | ≤10mm | ±1.0 | |||||
11—25mm | ±1.5 | ||||||
26—50mm | ±2.0 | ||||||
≥50mm | ±3.0 | ||||||
Free fall strength | Lossless rate ≥99% | ||||||
Compressive strength | φ3 | ≥250 | ≥300 | ≥350 | ≥400 | ≥500 | ≥500 |
φ6 | ≥800 | ≥1000 | ≥1000 | ≥1200 | ≥1500 | ≥1500 | |
φ8 | ≥1500 | ≥1600 | ≥1800 | ≥2000 | ≥2500 | ≥2500 | |
φ10 | ≥2000 | ≥2500 | ≥2800 | ≥3000 | ≥3500 | ≥3500 | |
φ13 | ≥3000 | ≥3000 | ≥3500 | ≥4000 | ≥5000 | ≥5000 | |
φ16 | ≥3500 | ≥4000 | ≥4500 | ≥5000 | ≥6000 | ≥7000 | |
φ20 | ≥6000 | ≥6000 | ≥7000 | ≥8000 | ≥10000 | ≥12000 | |
φ25 | ≥7000 | ≥7000 | ≥8000 | ≥10000 | ≥15000 | ≥17000 | |
φ30 | ≥8000 | ≥9000 | ≥10000 | ≥12000 | ≥17000 | ≥19000 | |
φ38 | ≥10000 | ≥12000 | ≥13000 | ≥15000 | ≥20000 | ≥22000 | |
φ50 | ≥12000 | ≥14000 | ≥16000 | ≥18000 | ≥22000 | ≥26000 | |
φ75 | ≥16000 | ≥18000 | ≥20000 | ≥22000 | ≥25000 | ≥30000 | |
50-75 | 55-75 | 60-80 | ≥80 | ≥82 | ≥85 | ||
Wear rate % | ≤2 | ≤1 | |||||
acid solubility,% | ≤6 | ||||||
Alkalinity,% | ≥77 | ≥85 | ≥90 | ≥92 | ≥95 | ≥97 | |
Refractoriness,℃ | ≥400 | ≥500 | ≥700 | ≥1000 | ≥1000 | ≥1000 | |
Resistant to sudden pressure difference | Non-destructive rate ≥ 99%, no change in compressive strength and pressure after sudden change is less than 25% | ||||||
Resistant to sudden temperature changes | Lossless rate≥99% | ||||||
Package | Iron drum packaging | Packed in iron drums, sealed with thick PP or PE plastic bags | |||||
Woven bag packaging | Available in sturdy and UV-resistant woven bags | ||||||
Note: Bulk density data is for reference only, not as a basis for acceptance. |
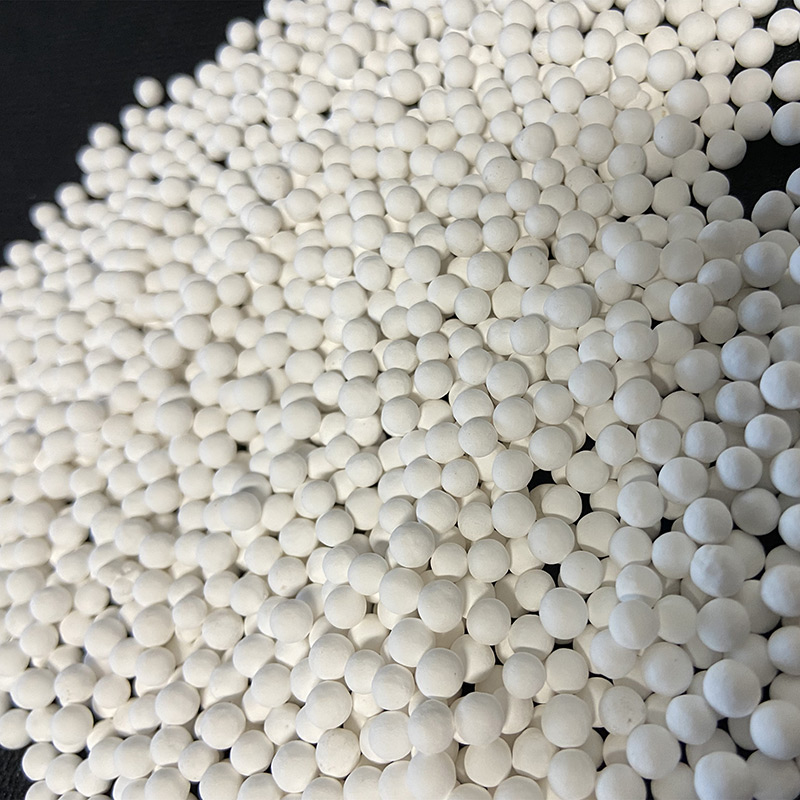
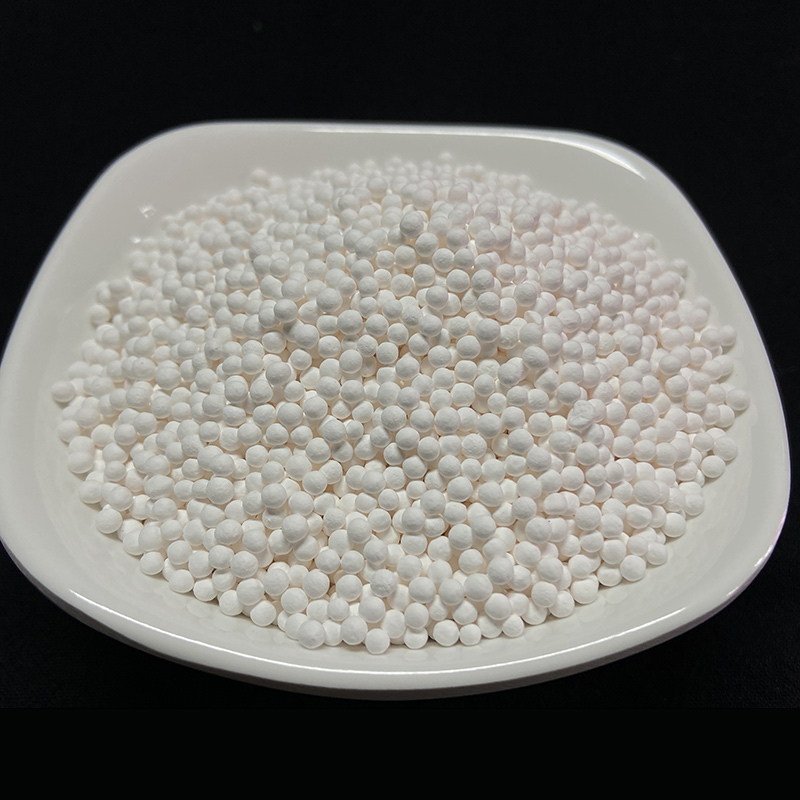
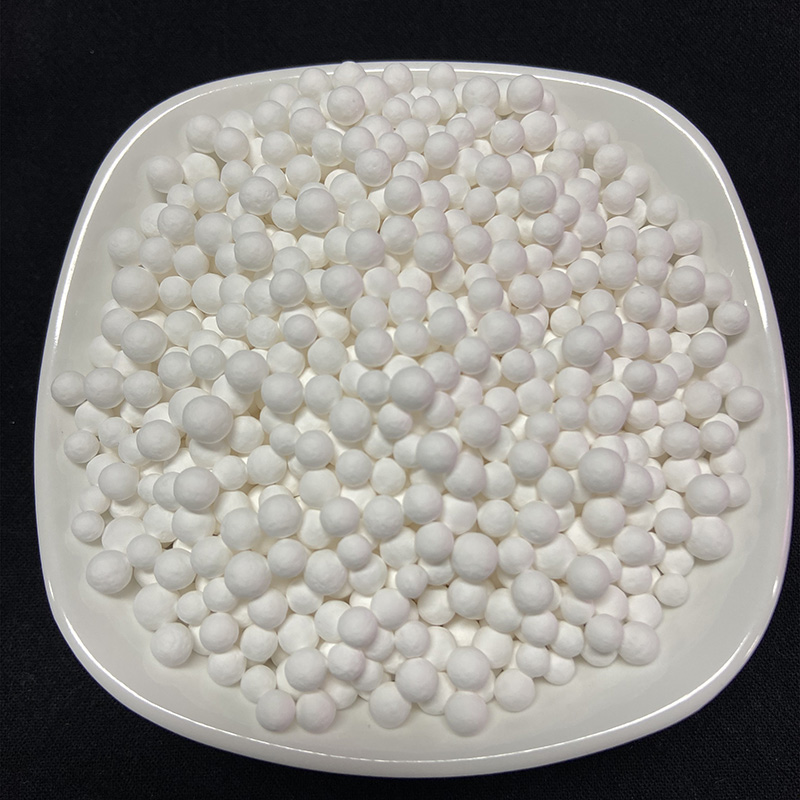
99 Filling Ball Water Absorption | ||
99 filler | diameter | diameter |
roll forming | φ<25mm | <5% |
Machine press forming | φ>25mm | <10% |
Al2O3 | ≥99% |
SiO2 | ≤0.14% |
Fe2O3 | ≤0.04% |
CaO +MgO | ≤0.03% |
TiO2 | ≤0.06% |
Na2O | ≤0.1% |
K2O | ≤0.1% |
CONDITION | INDEX |
load softening (yb/t370-1995) | Deformation under 0.2mpa pressure is less than 0.6% |
Thermal shock resistance (yb/t376.2-1995) | 1200°C down to 600°C. 10 times without surface cracks |
Reburn line changes (gb/t3997.1-1998) | 1400 ℃ for 12 hours, the maximum value is 0.25%, the average value is less than 0.20% |
Bulk density (gb/t2997-2000) | 3.2-3.50 g/cm3 |
crushing strength | Meet more than 230 kg/cm2 |
Apparent porosity | 12-18% |
Bulk density | 2.1-2.3g/cm3 |